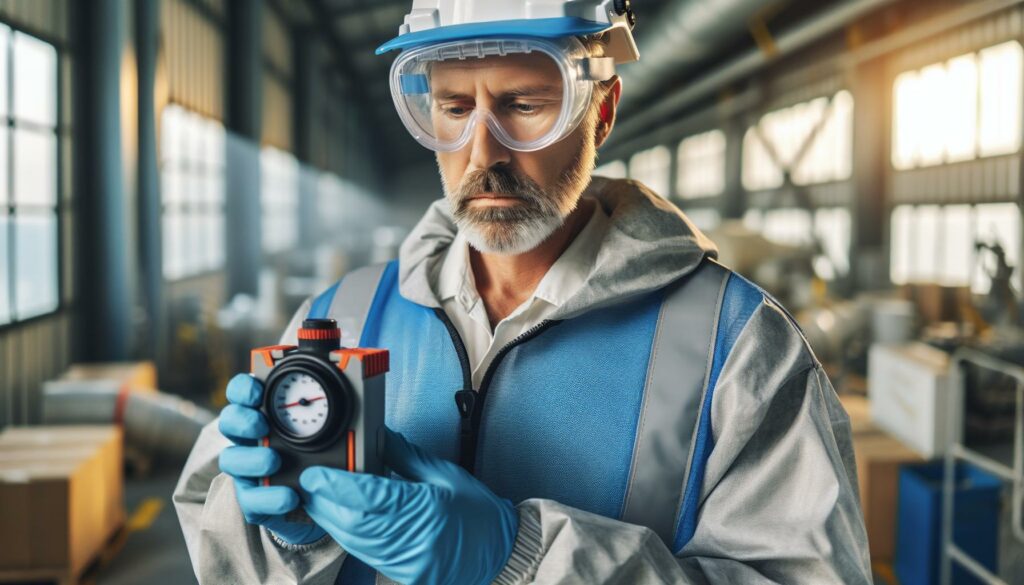
I’ve spent years studying workplace safety and can confidently say that industrial hygiene is the science of keeping yourself favorable to health, free from dirt, bacteria plays a crucial role in protecting workers’ health. It’s not just about keeping things clean – it’s a comprehensive scientific approach to identifying and controlling potential workplace hazards that could harm employees.
As an industrial hygiene is the science of keeping yourself favorable to health, free from dirt, bacteria specialist, I’ve witnessed firsthand how proper hygiene practices can dramatically reduce workplace illnesses and injuries. This field encompasses everything from monitoring air quality and controlling exposure to harmful substances to implementing effective sanitation protocols. By maintaining high standards of industrial hygiene we create safer more productive work environments while ensuring compliance with OSHA regulations and industry standards.
- Industrial hygiene is a scientific approach that focuses on identifying, evaluating, and controlling workplace hazards to protect worker health and safety.
- The field encompasses five key components: hazard identification, exposure measurement, control strategy development, preventive measure implementation, and continuous workplace monitoring.
- Common workplace hazards fall into four main categories: chemical (gases, vapors), physical (noise, radiation), biological (bacteria, viruses), and ergonomic (repetitive motions).
- Effective industrial hygiene relies on a hierarchy of controls, from hazard elimination to personal protective equipment (PPE), with proper documentation and monitoring systems in place.
- Creating a strong safety culture requires leadership commitment, employee engagement, and systematic implementation of safety protocols and training programs.
Industrial Hygiene is the Science of Keeping yourself Favorable to Health, Free from Dirt, Bacteria
Industrial hygiene is the science of keeping yourself favorable to health, free from dirt, bacteria encompasses the scientific practice of anticipating, recognizing, evaluating, and controlling workplace conditions that cause worker illness or injury. I specialize in applying these principles to protect workers from various occupational health hazards.
The American Board of Industrial Hygiene defines five key components of industrial hygiene:
- Identifying potential health risks in workplace environments
- Measuring exposure levels to chemical, physical, biological agents
- Developing control strategies to minimize hazardous exposures
- Implementing preventive measures through engineering solutions
- Monitoring workplace conditions to ensure ongoing safety
Here’s a breakdown of common workplace hazards addressed by industrial hygiene:
Hazard Type | Examples | Control Methods |
---|---|---|
Chemical | Gases, vapors, dusts | Ventilation systems |
Physical | Noise, radiation, heat | Barriers, PPE |
Biological | Bacteria, viruses, fungi | Sanitization protocols |
Ergonomic | Repetitive motions, posture | Workstation design |
Psychosocial | Stress, fatigue | Work organization |
The practice incorporates multiple scientific disciplines:
- Chemistry for analyzing air quality samples
- Physics for measuring radiation exposure
- Biology for assessing biological contamination
- Engineering for implementing control measures
- Ergonomics for optimizing workplace design
I employ quantitative methods to evaluate workplace exposures:
- Air sampling to measure airborne contaminants
- Noise monitoring to assess sound levels
- Surface testing to detect chemical residues
- Light measurements to evaluate illumination
- Temperature monitoring to assess heat stress
Through these systematic approaches, I help organizations maintain compliance with OSHA standards while protecting worker health through science-based methods and measurable results.
Key Principles of Industrial Workplace Health
Industrial hygiene is the science of keeping yourself favorable to health, free from dirt, bacteria workplace health relies on three fundamental principles that form the foundation of effective hazard management programs. I’ve observed these principles consistently produce measurable improvements in workplace safety outcomes across various industrial settings.
Hazard Recognition and Control
Recognition starts with systematic workplace evaluation to identify potential health risks from chemical, physical, biological, ergonomic or radiological sources. I implement a hierarchy of controls approach:
- Elimination: Removing the hazard completely from the workspace
- Substitution: Replacing dangerous materials with safer alternatives
- Engineering Controls: Installing ventilation systems, sound barriers or machine guards
- Administrative Controls: Rotating worker schedules, implementing safe work procedures
- Personal Protection: Using PPE as a last line of defense
Exposure Monitoring
Exposure monitoring involves quantitative measurement of workplace hazards through specialized equipment and techniques:
- Air sampling devices to measure airborne contaminants
- Noise dosimeters to track sound levels
- Direct-reading instruments for gases, vapors or radiation
- Wearable sensors to monitor personal exposure levels
- Documentation systems to track exposure data over time
- Respirators: N95 masks for dust, full-face respirators for chemicals
- Hearing Protection: Earplugs (NRR 25-33) or earmuffs (NRR 20-30)
- Eye Protection: Safety glasses, goggles or face shields
- Hand Protection: Chemical-resistant, cut-resistant or thermal gloves
- Body Protection: Chemical suits, flame-resistant clothing or high-visibility gear
PPE Type | Protection Level | Typical Applications |
---|---|---|
N95 Mask | 95% filtration | Dust, particles |
Earplugs | 25-33 NRR | High noise areas |
Safety Goggles | ANSI Z87.1 | Chemical splash |
Nitrile Gloves | Chemical resistant | Solvent handling |
Common Workplace Contaminants
In industrial hygiene is the science of keeping yourself favorable to health, free from dirt, bacteria settings, workplace contaminants pose significant health risks to employees through various exposure routes. These contaminants fall into distinct categories requiring specific control measures.
Chemical Agents
Chemical contaminants include volatile organic compounds, acids, bases, metals, solvents, pesticides, paints, oil mists, gases, fumes, particulates, vapors, and dusts. I’ve categorized the most prevalent chemical exposures encountered in industrial environments:
Chemical Category | Common Examples | Primary Health Effects |
---|---|---|
Organic Solvents | Benzene, Toluene | Respiratory issues, CNS damage |
Heavy Metals | Lead, Mercury | Neurological disorders |
Acids/Bases | Sulfuric acid, Sodium hydroxide | Chemical burns |
Industrial Gases | Carbon monoxide, Chlorine | Asphyxiation, Lung damage |
Biological Hazards
Biological contaminants consist of living organisms that cause infections or allergic reactions in workers. These include:
- Bacteria from contaminated water systems (Legionella pneumophila)
- Viruses transmitted through human contact (Influenza, SARS-CoV-2)
- Fungi growing in damp building materials (Aspergillus, Penicillium)
- Parasites present in contaminated soil or water (Giardia)
- Protein allergens from animal dander or plant materials
Physical Stressors
Physical contaminants create adverse conditions through energy transfer or environmental factors:
Stressor Type | Measurement Unit | Exposure Limit |
---|---|---|
Noise | Decibels (dBA) | 85 dBA (8-hour TWA) |
Radiation | Millisieverts (mSv) | 50 mSv annually |
Vibration | m/s² | 2.5 m/s² (8-hour limit) |
Heat | WBGT °C | 26-30°C (moderate work) |
- Direct tissue damage from radiation exposure
- Hearing loss from excessive noise levels
- Musculoskeletal disorders from vibration
- Heat stress from elevated temperatures
- Cold stress from low-temperature environments
Industrial Hygiene Best Practices
Industrial hygiene is the science of keeping yourself favorable to health, free from dirt, bacteria best practices encompass systematic approaches to maintaining workplace safety through proven methods and protocols. These practices focus on three critical areas: ventilation systems, equipment maintenance and comprehensive training programs.
Proper Ventilation Systems
Proper ventilation systems serve as the primary defense against airborne contaminants in industrial settings. Local exhaust ventilation systems capture contaminants at their source, while general ventilation systems maintain optimal air exchange rates of 6-12 air changes per hour. Key components include:
- Install capture hoods within 6-12 inches of emission sources
- Position makeup air inlets away from exhaust points
- Maintain negative pressure in contaminated areas
- Monitor airflow rates using anemometers monthly
- Clean ductwork every 3-6 months based on contamination levels
Regular Equipment Maintenance
Regular equipment maintenance prevents contamination through systematic inspection and repair protocols. Equipment maintenance schedules follow manufacturer specifications and industry standards to ensure optimal performance. Essential maintenance tasks include:
- Conduct daily visual inspections of safety equipment
- Test emergency eyewash stations weekly
- Calibrate monitoring instruments quarterly
- Replace HEPA filters at 75% loading capacity
- Document maintenance activities in digital logs
- Perform preventive maintenance on schedule
- Complete initial 8-hour safety orientation
- Participate in monthly toolbox talks
- Practice hands-on PPE fitting sessions
- Review safety data sheets quarterly
- Attend annual refresher courses
- Document all training activities digitally
- Validate comprehension through assessments
Health Monitoring and Documentation
Health monitoring systems track employee exposure levels to workplace hazards through systematic data collection protocols. I recommend implementing these essential monitoring components:
Medical Surveillance Programs
Medical surveillance encompasses routine health screenings specific to workplace exposures:
- Baseline examinations before job placement
- Annual physical evaluations with targeted testing
- Vision screening for workers using microscopes or detailed inspection tasks
- Hearing tests for employees in high-noise areas
- Respiratory function tests for those exposed to airborne contaminants
Exposure Documentation
A comprehensive exposure documentation system includes:
- Personal sampling data with time-weighted averages
- Area monitoring results from fixed sampling stations
- Incident reports detailing accidental exposures
- Equipment calibration records
- Exposure control maintenance logs
Record Retention Guidelines
These critical records require specific retention periods:
Record Type | Retention Period | Access Level |
---|---|---|
Medical Records | 30 years | Restricted |
Exposure Data | 30 years | Limited |
Training Documents | 3 years | General |
Incident Reports | 5 years | Limited |
Equipment Records | Life of equipment | General |
Digital Data Management
Modern digital systems enhance record accessibility through:
- Cloud-based storage with encrypted access
- Real-time exposure monitoring dashboards
- Automated compliance reporting
- Mobile data collection applications
- Integration with existing safety management systems
I maintain these records using OSHA-compliant documentation practices while ensuring data security protocols protect sensitive employee information.
Creating a Culture of Workplace Safety
A safety-focused workplace culture starts with clear communication protocols integrating industrial hygiene principles into daily operations. I’ve identified three essential components that form the foundation of a strong safety culture:
Leadership Commitment
Leaders demonstrate safety commitment through:
- Allocating resources for hygiene improvements
- Participating in safety walkthrough inspections
- Reviewing incident reports promptly
- Setting measurable safety performance goals
- Recognizing employees for safety contributions
Employee Engagement Programs
Effective engagement strategies include:
- Monthly safety committee meetings
- Peer safety observation programs
- Near-miss reporting systems
- Safety suggestion boxes
- Recognition programs for hazard identification
Performance Metrics
Key safety metrics to track:
Metric Type | Measurement Focus | Tracking Frequency |
---|---|---|
Leading | Safety training completion | Monthly |
Leading | Workplace inspections | Weekly |
Lagging | Incident rates | Monthly |
Lagging | Lost work days | Quarterly |
Process | Hazard corrections | Monthly |
Communication Channels
Safety information flows through:
- Digital safety dashboards
- Daily toolbox talks
- Safety alert notifications
- Department safety boards
- Mobile safety apps
Continuous Improvement
The improvement cycle includes:
- Regular safety audits
- Incident investigations
- Root cause analysis
- Corrective action tracking
- Program effectiveness reviews
This structured approach creates accountability while fostering employee participation in maintaining workplace hygiene standards.
I’ve seen firsthand how proper industrial hygiene is the science of keeping yourself favorable to health, free from dirt, bacteria practices transform workplaces into safer and healthier environments. By implementing comprehensive hazard control strategies monitoring systems and fostering a strong safety culture organizations can protect their most valuable asset – their employees.
The science of industrial hygiene continues to evolve with new technologies and best practices emerging regularly. I believe that staying committed to these principles isn’t just about meeting regulations – it’s about creating a workplace where everyone can thrive.
Remember that maintaining industrial hygiene is an ongoing journey that requires dedication collaboration and continuous improvement. When done right it’s an investment that pays dividends in employee health satisfaction and organizational success.